Player FM 앱으로 오프라인으로 전환하세요!
Episode 21 - Sam Ruben, Mighty Buildings
Manage episode 290592352 series 2523362
Listen to the episode
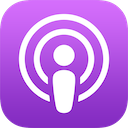
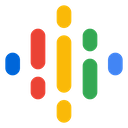

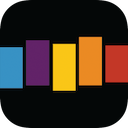
Transcript
Prefab Review
Hi, my name is Michael Frank and this is The Prefab Pod presented by Prefab Review, where we interview leading people and companies in the prefab housing industry. Today, we're speaking with Sam Ruben of Mighty Buildings, a company that makes small homes in the US out of California. Welcome, Sam.
Mighty Buildings
Thank you, Michael. It's great for the opportunity to be here.
Prefab Review
So I'm definitely excited to learn more about your company. But first, I was just hoping to learn a little bit more about you. How do you get into this business?
Mighty Buildings
Well, before Mighty Buildings, I was working as a sustainability consultant, having gone to Presidio Graduate School here in the Bay Area, which is one of the first programs in the world to center the entire curriculum around systems thinking and sustainability. And so I had been working with organizations, helping them optimize their impacts while: so impacts both in terms of sustainability, so environmental and social, as well as the impacts to the bottom line. So looking at everything from building envelopes to HVAC systems, LEDs to what's it mean to move a garbage can 10 feet and what's the impact on the waste disposal and recycling rates that way? And so it's been a really, really exciting journey and connected with my fellow co-founders who were originally at the time based in Singapore and had seen how they build there. In Singapore, the government owns all the housing, so they rebuild it every 20 or 30 years with the latest and greatest. And so they'd come here and they'd seen that we're still building, for the most part, using technologies one hundred twenty years old and just kind of blew their mind. And then for me, in terms of 3D printing and this is where it becomes obvious just how big a nerd I really am. I've been in love with 3D printing ever since I realized that Star Trek replicators, which has the atomic level 3D printing with energy modulation. And so as my capstone, as part of my capstone for my MBA, me and my team developed a business plan to take uncontaminated plastic hospital waste and convert it into 3D printer filament. And so when my my co-founders connected with a former classmate of mine who they worked with when she was at Indiegogo, they reached out to her to find out someone who could help them with the sustainability and the regulatory side of things. And she posted on one of our alumni Facebook pages. And I happened to reply, I think I may have actually even suggested a for another classmate who had been an advisor on my capstone. But I think he'd already taken a job like attaching smart cities or something. And then I met with our CEO, Slava, and he shared the idea with me and the vision. And just it made sense. And it was already clear to me that the world needs a better way to build both in terms of solving the housing crisis, but also doing so in a way that doesn't exacerbate the climate crisis. And so when he shared the vision that they had and the technology that was in development, it it clicked. And so I was really excited to join and I have been leading our compliance and certification, as well as our sustainability efforts ever since. And so I'm sure we will get into the regulatory side of things a bit more, because obviously with 3D printing, it's a new space and the building codes are literally written in blood. So it's imperative that we demonstrate that safety in code compliance. And we can talk about that in a bit.
Prefab Review
Yeah, totally. Just before we do, can you explain, and you can go to the Mighty Buildings website, MightyBuildings.Com to see some examples. But can you explain at your core, what you do?
Mighty Buildings
Yes. So what we do is we 3D print houses. We've been moving incrementally in how much of the units are 3D printed. Again, given the conservative nature of building regulators, just to make it as easy as possible at each step to say yes as we continue to build out our testing portfolio to demonstrate compliance and further use cases. But what we do is we've developed a unique material. It's a thermoset composite. So many people are familiar with corian by DuPont, which has been used as cladding and countertops since the 60s. And it's a similar class of materials. So it's effectively a synthetic stone without silica. But what we've done is we've developed a unique formulation and a unique production process that allows us to 3D print it. And what that means is that we use light to cure it. And so it allows us to print an entire three hundred fifty square foot studio shell in less than 24 hours. And so that's something we already have the ability to do. We're not delivering those units yet, again because of the regulatory side of things. But we will have that ability in short order based on the introduction of 3D printing into the building, into the 2021 international residential code as a part of Appendix AW, which is based on the new UL 3401 standard, which we are the first and only company and technology certified under it, and which was developed as a as a result of the process that you all went through in evaluating our technology for code compliance. And so with the 3D printing, with the light, what that means is the material cures quickly enough that it can support its own weight, which means that not only can we print the floors and the walls, but we also have the opportunity to print the roof and other unsupported spans. And it also allows us to have the ability to do free form design and bring more organic shapes into construction. And that's something we hint at with the curved wall on our ADUs that we're delivering currently, but something we're looking forward to continuing to develop into what our end goal, which is really to be a tool for an industry. And really be a production as a service platform to allow builders and developers to do more. Given the constraints that we're seeing on the material supply chain and on the labor force across the construction industry more broadly.
Prefab Review
That makes sense. In terms of what you make, you're basically making ADUs and small homes in California, exclusively?
Mighty Buildings
So our initial market has been accessory dwelling units and going direct to consumers. And the reason we chose the ADU market as our beachhead and kind of a starting point, is the changes in state law starting in 2016 that went to effect in 2017, which really streamlined it. And the simple fact that because of their size, somewhat cost prohibitive for most builders and developers unless they're doing many of them at the same time because of the overhead associated with that. And so what it also meant was that it was a space that we could demonstrate the viability of our technology, our compliance and certification portfolio without competing against the builders and developers who we've always seen as our end customers. And so along with what we're doing with ADUs, last month, we actually also announced our first BTB project, Villas, down in Rancho Mirage, which would be the initial phase will be 15 single family homes plus ADUs, and that'll actually be the world's first zero net energy 3D printed community. And we're looking to replicate that in a few different locations across California. And our long term vision is to actually have a distributed network of factories all across the United States and the world where we have demand and where we have partners so that we're not A exporting California construction cost to other states because that's just really silly, given how expensive it is to build here, but also that we're reducing those logistic costs, that we're able to take advantage of the local cost structures and most importantly, that we're creating jobs for that local market. Because one of the really cool things about using 3D printing robotics, because the 3D printing is actually the first step. So we have the world's largest light based printing system in which we can print up to a 450 square foot footprint and up to a 3,700 cubic foot volume, which means we're actually more limited by over road transport than we are by the actual print volume. And then it goes from there to our robotic finishing cell where because of the nature of our material, well, first we have a 3D scanning attachment which scans the object or the module to make sure that it matches the digital file that it was based off of, while also creating an exact digital copy of the physical object itself in order to create toolbars for post processing. So after the scan, we switch to an attachment that has a CNC head because even the raw material is really strong. We are able to mill it using CNC heads that are normally used in metals like aluminum, copper, and we're able to use that so we can either leave the beautiful printed surface, which some people really, really like and actually are willing to pay a lot of money to have done on traditional materials. Or we can mill it so it is a sort of smooth stone like finish. And it also opened up a future possibilities of increased design versatility, both from the 3D printing and the ability to print different forms, but also the ability to do things like mimic brickwork or mimic siding based on how we mill the surface or even create facade looks that have never been seen before. And so that's something that we're where we're going is to really unlock that versatility of design and really unlock that creativity. And so we have a rapid plugin that allows designer developers and builders to work with a new panel system, which we call it we call the mighty kit system, kind of like the Sears kit home for the twenty first century and the mighty house line that we have and that we're using for the villa project with our group down in Rancho Mirage and Coachella Valley is the first deployment of that. And those mighty houses have been designed by architects out of Los Angeles, one of the world's leading modern design firms and also in partnership with one of the world's leading engineering firms. And so that's been really exciting. And the first deployment of that and in the future with that plug in the plan is to continue to develop it, to actually allow designers to work directly with our technology, opening up that ability to do free form because we already have a software stack that can take 3D models and convert them into printable objects.
Prefab Review
So in terms of 3D printing, when we talk about the vectors of benefit, right. Like you talked about design, you've talked a little bit about potentially the sustainability of the materials. Is there a cost advantage here right now as well?
Mighty Buildings
There is, yeah. So right now the units we're delivering are type two summer luxury and we're able to deliver them for about 40 percent less than comparable stick built. And then in the sustainability side, because we're using 3D printing, we're able to print only what we need. So where we are right now, it's about 95 percent waste diversion. We're in the process of adding the ability to capture the milled material from the milling process, and we use that as filler and new material at that point will be over 99 percent elimination of waste that you would see from a traditional build. So that's two to five tons of carbon. Because we're eliminating three to five pounds per square foot that would normally go to landfill in a traditional build.
Prefab Review
Got it, I've seen you started out with these modular buildings and then you talked about sort of your kit system, which it looks like are both sort of apparent in your homes. And I guess in sort of the more interoperable stuff you talked about in terms of the plug in with Rabid and other architects. Why why kits versus modular for all this? Is it just greater flexibility?
Mighty Buildings
Yeah. So it opens up additional opportunities. Because one of the things that we've learned in delivering modules is that as amazing as they are and as quick as I mean, we have the ability with our studios, which are a single model, even with our duos, which are two models, to have those set in a day and fully installed in about a week. So they're amazing for that. And fully finished ready to go. But you generally need cranes and cranes and power lines do not play well, and once you start getting into removing power lines, it gets very expensive and you start seeing potential timeline extensions of six months or more in order to get those permits. And so it means that with modules we're limited in where we can deliver and with the kit system, it allows us to increase that flexibility because with the kits where we only need about six feet to get into a backyard versus the ability to crane over. And so that's a huge opportunity to address a larger market, as well as to demonstrate the versatility of our production system. Because, again, where we're going is really a design and product agnostic production as a service platform. And so having the ability to do modules, having the ability to do panels really opens up a variety of design possibilities, as well as delivery opportunities that can be customized to the needs of a specific project.
Prefab Review
Got it. So why user facing it all at this point? Just because you need to bring proof of concept? We should talk about your service offering in general to consumers, but, you know, coordinating all these different parts is a lot of work.
Mighty Buildings
That it is.
Prefab Review
It's much more work than just being a technology provider. So, yeah. Why do that?
Mighty Buildings
Yeah, and you're right, because we also do offer a full turnkey experience for our customers where we handle the entitlements, we handle coordination of site work, all of that to make it as easy and as painless as possible. But yeah, you're right, a lot of it basically was to allow us to have the chance to prove the viability of the technology, prove the market fit because most builders and developers tend to be conservative, understandably so, they tend to be risk averse. And so when it comes to new technology, there's some reticence to be the first mover and to be the first one that's taking it up. And so by being able to demonstrate that we can do it with homeowners, it has opened up those other opportunities on the B2B side, especially ever since we announced the Villas project, that interest has gone up even more. That said, we've been talking with some of the biggest builders from the very beginning. And so there are ongoing conversations there that as we demonstrate the ability to deliver and the ability to scale, those will definitely pick up.
Prefab Review
So if I'm thinking about your product lines right now and I'm looking at the fact that you are, it looks like you're also continuing to expand your product line in general.
Mighty Buildings
Exactly. We started with ADUs now we're also offering single family homes. And our goal is hopefully by end of next year to be doing low rise multifamily. So townhouses and three to six story low rise apartment buildings using our new fiber reinforced version of our material that we're moving into a certification later this year.
Prefab Review
And then in terms of your actual, like single family homes and your current products, it sounds obviously you're saying that your technology is infinitely flexible. But if I'm a consumer and I'm a homeowner, like particularly for single, I mean, if you're in the Bay Area, we do a lot of products in the Bay Area. And one of the I would say not my favorite parts of the process is the design review process in some areas. So, like, if I'm trying to build a single family home, even if I really wanted to look this way. Right. Like I might get substantial feedback, how much flexibility if I'm a consumer, do you all sort of so provide me with, you know, design.
Mighty Buildings
Where we are now, it's relatively limited. I mean, particularly because we are operating with state approved plans, which means that we're getting the building permit for at the state level rather than when we get to local level it's more, say, permits for the site work. And then also, as you mentioned, design review and planning and plan checks were zoning purposes.
Prefab Review
And that's true for single family home kits as well? Or are you just kind of on the ADU side?
Mighty Buildings
Well the kits are nice because they have the opportunity to either be certified under the state or with the local authority, depending what makes the most sense, because we also do have the ability or one of the things we're working on is that ability to also to preassemble the kits into modules for sites where that makes sense too. So that also adds to the versatility.
Prefab Review
So that's essentially the same thing as modular.
Mighty Buildings
Exactly. And so one of the things with that versatility is that ability to kind of approach it, the permitting and entitlement process from the route that makes the most sense.
Prefab Review
Right. And because I've found a kit and I don't know what your experiences are. Modular is considerably more complicated to get financed than kits in our experience, just because of the, and maybe it's not different for you, but we we've seen like draw schedules and stuff just be a little, there's a wider variety of lenders we use for when we're doing kit builds then for modular builds.
Mighty Buildings
For ours it's been, I mean well it also depends if the modular is modular or if it's manufactured.
Prefab Review
I mean like non-HUD.
Mighty Buildings
Yeah. For us we haven't noticed a ton of difference yet, but it'll be interesting to see how that changes over time because obviously having those comps makes a huge, huge difference. And so where you're building can often really impact how easy that financing is.
Prefab Review
So in terms of flexibility, just because I mean, I'm looking at the homes on your website right now.
Mighty Buildings
Yeah, it's right now. It is pretty limited.
Prefab Review
So if I wanted to change floor plans within a shell is that kind of, like is it basically only cosmetics, but like any kind of floorplan structure is out?
Mighty Buildings
If you're a B2C customer, we do have some limited customization that we can do. And depending on the project, it's something we can discuss. If it's a developer builder, there's a much greater opportunity to do that because then obviously we're doing a number of units at a time and so more scale and then it makes more sense to go through the process of getting the approval for a new design. But in the future, yeah, the goal is to have a much higher level of customization possible and a lot of those cases will actually be working with builders, developers and kind of doing a white label. Some of them may be custom home builders who are doing larger projects and single family homes, one off. And then some of them will be more developers who are doing a number of units at once. But the goal is eventually to kind of be able to offer that level of versatility, but for where we are, it's not efficient for us to do so yet.
Prefab Review
Looking at your existing product line, can these go on any kind of foundation? Like, I know you're in Oakland and we've done projects in kind of Oakland Hills, Berkeley Hills, and you see a ton of like post and pier foundations and other such things because they sort of it's both kind of the style.
Mighty Buildings
But yeah, I mean, the versatility and all the different soil types. And then, like, if you don't want to do, how much grading do you want to do, or have to do. And so, yes, we designed our modules. I think we already have designs for seven different foundation types, including helical piers and everything we've delivered so far has made sense to do as a slab. But yeah, we do have that ability to adapt to different foundation types depending on the needs of the specific site.
Prefab Review
Got it. So the question we get most, which is riddled with nuance. But that's OK. We'll do the best we can here around cost. So like I'm looking at your website right now and I'm looking at like, let's say, the mighty duo ADU, which is 700 square feet. If we assume that you're installing that in an expensive area, which are probably almost exclusively areas you work in if you're located in Oakland. But, you know, let's say like a flat lot.
Mighty Buildings
Well, I mean we've delivered units to East Oakland. We've delivered units all across the Bay Area, San Diego. So it really doesn't make a difference as far as the neighborhood. We got interest from all over and they're able to deliver.
Prefab Review
Cool, OK, so I just meant like an area. If you were moving units to Riverside County, at least the local area, labor might be a bit different than like.
Mighty Buildings
Yeah, and we do notice that for particularly when we're looking at the full turn-key, we often are able to provide lower final estimates in Southern California than we are for our projects here in Northern California. And that just reflects the nature of the subcontractors for the site work and everything.
Prefab Review
But so let's say I'm talking about building the Duo B, which is like your 700 square foot, one and two bedroom. Can you help me? And I mean, you're really good about sort of breaking down, like starting at prices. But can you sort of explain, like, what you would expect, like a typical build to come out at assuming right, a flat lot And just explain kind of where the cost variabilities are, because I assume the local labor is probably the biggest one.
Mighty Buildings
So, yeah, so the unit itself, a two bedroom, I think we're selling the two modules fully furnished, including a washer-dryer, induction cooktop, dishwasher, everything. High-end finishes, beautiful bathroom, lots of storage. So that is with the two bedroom version, I believe $169,000 for just the unit itself. Right. And then we generally see 30 to 40
Prefab Review
And that is just the module, not including anything else?
Mighty Buildings
Exactly, not counting the site work, not counting the entitlements, not counting any of the delivery, installation. And we generally see about 30 to 40 percent on top of that. So that's where the starting at $255,500 you see on our website for starting out is generally what we see on average. And so that's kind of where that starts. That's going to be more or less what it's going to be for a pretty basic site where it's easy access, flat lot, a community that doesn't have particularly high fees, which obviously now that states cap those in most cases under
Prefab Review
Under seven forty nine, right?
Mighty Buildings
And so where it starts to get expensive is on sites that maybe are on hills, that require grading, that might have a retaining wall that may require or if perhaps it's a site where you've maxed out your utilities and you need to add in another utility box or upgrade your sewer line. So those are obviously things that can add significant costs. But if it's just straightforward, it's pretty, pretty basic. And once the entitlements are in hand, we can have it on the ground and completed in less than a month.
Prefab Review
Are you including solar on those?
Mighty Buildings
They are solar ready and we do have an upgrade available for solar.
Prefab Review
Is it necessary though? I'm sure you're much more knowledgeable on title 24.
Mighty Buildings
Yeah, so it has to be at least solar ready. And then the homeowner is required to install solar, though depending what the shading looks like, that can impact how much solar they're actually required to install. And it also depends because some of our units are actually approved under the previous codes, like I'm ready studio design is basically my studio design. And some of those variations of that actually don't require solar because they were approved under the previous building code and which is good for three years that approval of those ones. So it really varies. But yeah, but we do offer it and we are looking at kind of also offering battery storage to be able to take it off grid because it is, they are pretty efficient. The amount of energy required is relatively low. And so it's yeah, it's definitely an opportunity. And I mean, part of it, like with the Villa project, those are zero net energy because we are both the energy efficiency, but then also the inclusion of solar and the inclusion of battery storage to add not only resiliency, but then further ensure full title 24 compliance and going beyond that to zero net energy.
Prefab Review
And you said all your building is happening out of your Oakland facility right now?
Mighty Buildings
Currently. Correct.
Prefab Review
And obviously, I would say there's one or two companies that we work with that do a bit of construction out of L.A., but part of the idea of prefab or modular, it seems like it's to take advantage of lower cost labor pools. Right. So, you know, as I said, locate your factory in Utah or in Riverside.
Mighty Buildings
Right. I mean, that's why a number of the manufacturers here in California. They're being built in Washington or Idaho.
Prefab Review
Yeah, exactly. I imagine margin matters a little bit for larger builders. So I imagine the ability to just have lower cost inputs probably helps a lot in that stuff. So is that on the roadmap for you all to kind of locate somewhere, in kind of a more rural area probably, or at least a less coastal area?
Mighty Buildings
Sort of. So we're not trying to race to the bottom. What we're doing really is helping the existing labor force build more. Where we're able to capture significant savings per unit is that we can eliminate up to 90 percent of the labor hours and really optimize it so that the human touch is being used for the parts that make sense. In doing so, we're also looking to increase productivity by as much as 20 times. So at the end of the day, we're actually hoping to create more work. And so for us, because of the way we kept our savings, it's not as important to be setting up in rural areas. And in fact, that's one of the things that we can do that you really can't do with traditional prefab and still be cost efficient is that where we are in Oakland. We're in an old Peet's Coffee Warehouse by the Colosseum. So we're in the heart of an industrial center. We were able to find an empty warehouse space that we can take advantage of and not need to build hundreds of thousands of square feet or a million square feet out in a rural or semi-rural area that's far from demand and far from your labor pool. We can actually set up near that demand and use that labor pool while still being efficient. And so that's one of the real big advantages. So our vision is actually a distributed network of factories around the country and around the world, like looking at places like Phoenix, like Detroit, like Pittsburgh, like Seattle, and really being able to set up factories using existing warehouse space. So we're not having to build a bespoke factory, you can actually spin up a factory in three to six months, a relatively low cost, and serve that market and create new jobs for that market. So we're not necessarily trying to avoid the labor. We're actually just trying to think what that labor looks like and what where it makes sense and in order to maximize its value.
Prefab Review
That makes sense. Got it, and then in terms of actually the fulfillment of your existing homes, have you just built a builder network around California to actually do the kind of local foundation and site work and all that stuff?
Mighty Buildings
Yes, we've got a network of contractors that we work with across the state who we've vetted and trained. And we also provide additional tools to make it easy and to help ensure that we get first time right on the foundation every time and make it as cookie cutter and IKEA easy as possible.
Prefab Review
Is there any special training they need to do?
Mighty Buildings
Yeah, no, no special training. I mean, everything they're doing is things that they already know how to do. But we've been looking at how we can help optimize things for them. So providing various forms and things like that just make their lives as easy as possible and also help ensure that it minimizes any rework that's necessary. So in that regard, we're looking at both digital tools, but then also physical things, like what it looks like to create a form or have custom form work for the concrete that we provide to make sure that it is exactly what it's supposed to be. Things like that.
Prefab Review
And you have some details of this on your website. So sorry for the redundancy. From a timing perspective, is the time to build these pretty similar to, you know, most modular and prefab homes?
Mighty Buildings
I mean, we can build the unit in about a week. So once we have permits in hand, we can have a unit fully installed in under a month. I mean, the biggest variable in the entitlement process is the permitting. On our end. We've got it, we've got it locked. Like, once those permits are in hand, we're good to go. We can do it in a month. The issue is that those permit timelines are still incredibly variable. I mean, we've had permits that have taken a week. We've had permits that have taken six months.
Prefab Review
I mean, the state of California has 60 days to get feedback. Right?
Mighty Buildings
They have to take some sort of action within 60 days. And so some of it comes down to , one of the few benefits we've seen from the pandemic is the digitization of planning departments. So that's been a great move. But we're also still dealing with that. They're still dealing with large backlogs and they're doing everything they can. But it's still moving slower than I mean, and from talking with city officials, I mean, it's slower than they want it to be. Like they're not trying to make it slow. It's just the reality of where things are for a lot of projects right now. But they're working on getting better. And part of it is also taking advantage of opportunities like pre-approved plans in places like L.A. and San Jose and others. And so that's one of the methods that we are working on and getting out. And we believe either some have been approved or are in the process of and will be posted there shortly. And so we're looking at ways we can accelerate that way also through just developing that relationship with the local officials because they want to get more housing. I mean, with the regional housing needs allocations as they are, ADUs have become so much more important in helping cities avoid massive fines and lawsuits. So there's real opportunities. But we also have to do education around the fact to build housing programs. We provide an educational packet around who is responsible for what phase of the approval. So there is also an educational component both because of the 3D but because of the familiarity with the approval process for our homes.
Prefab Review
That's awesome and great to learn a little about Mighty Buildings. I want to quickly transition to our fire round where we sort of ask a question to the extent you ca,n answer in one minute or less.
Mighty Buildings
Fire away, I feel like we should be eating hot wings.
Prefab Review
There should be a siren or something. So I guess the first thing is sort of in terms of evaluating sites. I mean, this is a particularly Bay Area, L.A. question we get a lot, which is I'd love to do an ADU. I don't know if my sight is too steep, et cetera. What are the things that homeowners should look for?
Mighty Buildings
Power lines. At least if you're looking to do modular, understanding where the power lines are is a big part of it. Understanding what kind of access you have to the backyard where if you're building with modular, think through like, is there an opportunity, maybe you have a neighbor who has easy access to that location through their driveway or something. And so it's looking for those opportunities. But then also thinking through how steep is it? What kind of soil might you have? What kind of foundation is going to be required? Is it going to require an extensive retaining wall? And these are all things that we help with. So if they're interested and they're not sure, they should reach out to us because we have a wonderful compliance team that does, one of the first things we do, is that we take a look at the site. First we start on Google Maps to do a basic quick understanding of the feasibility, and then we actually send out one of our local partners to confirm what we've learned on the site and look at things like the utilities, understanding the capacity there, whether any upgrades will be required and the viability of the site in terms of delivery and installation.
Prefab Review
OK, that makes sense. In terms of sustainability, we get a lot of press releases from companies claiming a new breakthrough in sustainability and just like in the same way on construction, we get a lot of press releases where people are like, you know, now we cut to one one-thousandth of a millimeter. And this is precision like you've never seen before. So one of the things that we sort of are to figure out is how do we, like, sort of cut through the marketing speak and evaluate what really matters? How would you say on a sustainability process that homeowners who want to kind of live their values, what should they look for?
Mighty Buildings
Yeah, so they should be looking and be asking about how much waste is generated during the construction phase, because that's kind of an often hidden sustainability impact. They should be looking at what kind of energy efficiency does it provide or what are the potential savings to their energy bill? Because, I mean, that's all because the cool thing about sustainability, particularly in terms of energy efficiency and the ability to do zero net energy, is that not only does it have amazing impacts in terms of carbon, I think a zero net energy home in California saves on average about 400 kilograms of carbon a month. So you're looking at like four tons of carbon, almost five tons of carbon a year, but then also looking at about $115 in savings per month on average on the cost. So that's one area, is what's the actual energy efficiency and the performance of it there? And then you should also be looking at things like what's the embodied carbon of the material and what's being used? And I'll admit there, that's one area that we're currently higher than we want to be. But we've also committed to being carbon neutral by 2028 and going beyond that and really shooting for carbon negativity by 2040. So one of the things that we're actively doing right now is we're certifying a new material that has lower carbon. We're identifying new possibilities for further improvements through incorporation of things like recycled materials, as well as continued improvement in terms of strength to allow us to use less material and reduce the carbon impact in that way. But then also what happens at the end of life? Because that's when we're thinking about it, we actually have incorporated lifecycle assessment into our design phase, both in terms of new material as well as new designs. And when we do that, we're not just looking cradle to gate. So we're not just cradle to foundation, we're not looking to just when it's installed, but we're looking all the way to the end of life. And so currently we have the ability to recycle our material, to grind our material up, and we use it as filler. We're looking fifty, a hundred years down the line, but we're already thinking about it. And in the future we're looking at opportunities to go beyond that. And so we're also incorporating obviously design for assembly and for manufacturability and assembly, which is a key part of any manufacturing process, but also adding into that disassembly and reuse. So what's it look like to identify opportunities for reusing the material and end of life? Because it's really important that we're avoiding that landfill at the end, even if it's fifty or a hundred years from now.
Prefab Review
That makes sense. What are the use cases that people are actually using your homes for now? Is it mostly like, "I want a little more room in my house, I want an office" or you've seen people doing this for investment purposes as well?
Mighty Buildings
It runs the gamut. So we've had customers, some who are landlords who want to add an additional unit to an existing rental property to provide more rental options. People who are homeowners who have added a unit to turn that into a rental property and have that income generation people have used them as pool houses, multigenerational living both in terms of younger people moving back, as well as parents kind of moving in as they downsize, guestrooms, as you say, home offices, needing more space. So it really runs the gamut.
Prefab Review
OK, that makes sense. OK, this has been awesome. You definitely passed the fire round.
Mighty Buildings
Oh, good.
Prefab Review
I know you're concerned about that. The final question we ask this to everyone, is what are you excited about for your company or the industry in the near future?
Mighty Buildings
Yeah. So for us I'm really excited about this new project in Rancho Mirage and our step into B2B and really helping become that tool that can unlock the productivity needed while not exacerbating the climate crisis. And more broadly for the industry, I'm really excited by some of the exciting initiatives that are out there, like the Advanced Building Construction Collaborative that's working on either launching or is going to be launched shortly to help unlock productivity in the American offsite construction sector, similar to what was done for silicon chips back in the 90s, because there's a huge new opportunity there. And so it's been really exciting. I'm seeing a lot of stuff happening through, like the Housing Innovation Alliance, a lot of interesting conversations happening about healthy buildings and the build to rent market as kind of growing opportunities, particularly in areas where you have more land and where it's not necessarily competing as much on kind of sensitive environmental areas. So it's definitely some really interesting conversations. And it's great to see the industry really moving towards embracing new technologies as a way to solve the crisis while mitigating those climate crisis impacts.
Prefab Review
That's awesome. Yeah, I agree and we appreciate all the work you all are doing to push this forward. So thanks again, Sam. For more information about Sam and Mighty Buildings, visit mightybuildings.com. And you can also always visit us at prefabreview.com. Thanks again.
Mighty Buildings
Thanks so much, Michael.
Get Our Guide to Buying a Prefab House
Learn how to buy land, select the best house plan, get financing, calculate investment ROI, and more. Save hundreds of hours of research.
We respect your privacy.
Thank you! The guide will be emailed to you soon.
If you want even more support with your project, then signup for Prefab Concierge - our free service where you are paired with a member of our staff who provides you 1:1 support with your potential project -> Learn More
39 에피소드
Manage episode 290592352 series 2523362
Listen to the episode
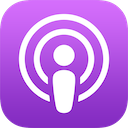
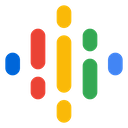

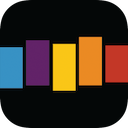
Transcript
Prefab Review
Hi, my name is Michael Frank and this is The Prefab Pod presented by Prefab Review, where we interview leading people and companies in the prefab housing industry. Today, we're speaking with Sam Ruben of Mighty Buildings, a company that makes small homes in the US out of California. Welcome, Sam.
Mighty Buildings
Thank you, Michael. It's great for the opportunity to be here.
Prefab Review
So I'm definitely excited to learn more about your company. But first, I was just hoping to learn a little bit more about you. How do you get into this business?
Mighty Buildings
Well, before Mighty Buildings, I was working as a sustainability consultant, having gone to Presidio Graduate School here in the Bay Area, which is one of the first programs in the world to center the entire curriculum around systems thinking and sustainability. And so I had been working with organizations, helping them optimize their impacts while: so impacts both in terms of sustainability, so environmental and social, as well as the impacts to the bottom line. So looking at everything from building envelopes to HVAC systems, LEDs to what's it mean to move a garbage can 10 feet and what's the impact on the waste disposal and recycling rates that way? And so it's been a really, really exciting journey and connected with my fellow co-founders who were originally at the time based in Singapore and had seen how they build there. In Singapore, the government owns all the housing, so they rebuild it every 20 or 30 years with the latest and greatest. And so they'd come here and they'd seen that we're still building, for the most part, using technologies one hundred twenty years old and just kind of blew their mind. And then for me, in terms of 3D printing and this is where it becomes obvious just how big a nerd I really am. I've been in love with 3D printing ever since I realized that Star Trek replicators, which has the atomic level 3D printing with energy modulation. And so as my capstone, as part of my capstone for my MBA, me and my team developed a business plan to take uncontaminated plastic hospital waste and convert it into 3D printer filament. And so when my my co-founders connected with a former classmate of mine who they worked with when she was at Indiegogo, they reached out to her to find out someone who could help them with the sustainability and the regulatory side of things. And she posted on one of our alumni Facebook pages. And I happened to reply, I think I may have actually even suggested a for another classmate who had been an advisor on my capstone. But I think he'd already taken a job like attaching smart cities or something. And then I met with our CEO, Slava, and he shared the idea with me and the vision. And just it made sense. And it was already clear to me that the world needs a better way to build both in terms of solving the housing crisis, but also doing so in a way that doesn't exacerbate the climate crisis. And so when he shared the vision that they had and the technology that was in development, it it clicked. And so I was really excited to join and I have been leading our compliance and certification, as well as our sustainability efforts ever since. And so I'm sure we will get into the regulatory side of things a bit more, because obviously with 3D printing, it's a new space and the building codes are literally written in blood. So it's imperative that we demonstrate that safety in code compliance. And we can talk about that in a bit.
Prefab Review
Yeah, totally. Just before we do, can you explain, and you can go to the Mighty Buildings website, MightyBuildings.Com to see some examples. But can you explain at your core, what you do?
Mighty Buildings
Yes. So what we do is we 3D print houses. We've been moving incrementally in how much of the units are 3D printed. Again, given the conservative nature of building regulators, just to make it as easy as possible at each step to say yes as we continue to build out our testing portfolio to demonstrate compliance and further use cases. But what we do is we've developed a unique material. It's a thermoset composite. So many people are familiar with corian by DuPont, which has been used as cladding and countertops since the 60s. And it's a similar class of materials. So it's effectively a synthetic stone without silica. But what we've done is we've developed a unique formulation and a unique production process that allows us to 3D print it. And what that means is that we use light to cure it. And so it allows us to print an entire three hundred fifty square foot studio shell in less than 24 hours. And so that's something we already have the ability to do. We're not delivering those units yet, again because of the regulatory side of things. But we will have that ability in short order based on the introduction of 3D printing into the building, into the 2021 international residential code as a part of Appendix AW, which is based on the new UL 3401 standard, which we are the first and only company and technology certified under it, and which was developed as a as a result of the process that you all went through in evaluating our technology for code compliance. And so with the 3D printing, with the light, what that means is the material cures quickly enough that it can support its own weight, which means that not only can we print the floors and the walls, but we also have the opportunity to print the roof and other unsupported spans. And it also allows us to have the ability to do free form design and bring more organic shapes into construction. And that's something we hint at with the curved wall on our ADUs that we're delivering currently, but something we're looking forward to continuing to develop into what our end goal, which is really to be a tool for an industry. And really be a production as a service platform to allow builders and developers to do more. Given the constraints that we're seeing on the material supply chain and on the labor force across the construction industry more broadly.
Prefab Review
That makes sense. In terms of what you make, you're basically making ADUs and small homes in California, exclusively?
Mighty Buildings
So our initial market has been accessory dwelling units and going direct to consumers. And the reason we chose the ADU market as our beachhead and kind of a starting point, is the changes in state law starting in 2016 that went to effect in 2017, which really streamlined it. And the simple fact that because of their size, somewhat cost prohibitive for most builders and developers unless they're doing many of them at the same time because of the overhead associated with that. And so what it also meant was that it was a space that we could demonstrate the viability of our technology, our compliance and certification portfolio without competing against the builders and developers who we've always seen as our end customers. And so along with what we're doing with ADUs, last month, we actually also announced our first BTB project, Villas, down in Rancho Mirage, which would be the initial phase will be 15 single family homes plus ADUs, and that'll actually be the world's first zero net energy 3D printed community. And we're looking to replicate that in a few different locations across California. And our long term vision is to actually have a distributed network of factories all across the United States and the world where we have demand and where we have partners so that we're not A exporting California construction cost to other states because that's just really silly, given how expensive it is to build here, but also that we're reducing those logistic costs, that we're able to take advantage of the local cost structures and most importantly, that we're creating jobs for that local market. Because one of the really cool things about using 3D printing robotics, because the 3D printing is actually the first step. So we have the world's largest light based printing system in which we can print up to a 450 square foot footprint and up to a 3,700 cubic foot volume, which means we're actually more limited by over road transport than we are by the actual print volume. And then it goes from there to our robotic finishing cell where because of the nature of our material, well, first we have a 3D scanning attachment which scans the object or the module to make sure that it matches the digital file that it was based off of, while also creating an exact digital copy of the physical object itself in order to create toolbars for post processing. So after the scan, we switch to an attachment that has a CNC head because even the raw material is really strong. We are able to mill it using CNC heads that are normally used in metals like aluminum, copper, and we're able to use that so we can either leave the beautiful printed surface, which some people really, really like and actually are willing to pay a lot of money to have done on traditional materials. Or we can mill it so it is a sort of smooth stone like finish. And it also opened up a future possibilities of increased design versatility, both from the 3D printing and the ability to print different forms, but also the ability to do things like mimic brickwork or mimic siding based on how we mill the surface or even create facade looks that have never been seen before. And so that's something that we're where we're going is to really unlock that versatility of design and really unlock that creativity. And so we have a rapid plugin that allows designer developers and builders to work with a new panel system, which we call it we call the mighty kit system, kind of like the Sears kit home for the twenty first century and the mighty house line that we have and that we're using for the villa project with our group down in Rancho Mirage and Coachella Valley is the first deployment of that. And those mighty houses have been designed by architects out of Los Angeles, one of the world's leading modern design firms and also in partnership with one of the world's leading engineering firms. And so that's been really exciting. And the first deployment of that and in the future with that plug in the plan is to continue to develop it, to actually allow designers to work directly with our technology, opening up that ability to do free form because we already have a software stack that can take 3D models and convert them into printable objects.
Prefab Review
So in terms of 3D printing, when we talk about the vectors of benefit, right. Like you talked about design, you've talked a little bit about potentially the sustainability of the materials. Is there a cost advantage here right now as well?
Mighty Buildings
There is, yeah. So right now the units we're delivering are type two summer luxury and we're able to deliver them for about 40 percent less than comparable stick built. And then in the sustainability side, because we're using 3D printing, we're able to print only what we need. So where we are right now, it's about 95 percent waste diversion. We're in the process of adding the ability to capture the milled material from the milling process, and we use that as filler and new material at that point will be over 99 percent elimination of waste that you would see from a traditional build. So that's two to five tons of carbon. Because we're eliminating three to five pounds per square foot that would normally go to landfill in a traditional build.
Prefab Review
Got it, I've seen you started out with these modular buildings and then you talked about sort of your kit system, which it looks like are both sort of apparent in your homes. And I guess in sort of the more interoperable stuff you talked about in terms of the plug in with Rabid and other architects. Why why kits versus modular for all this? Is it just greater flexibility?
Mighty Buildings
Yeah. So it opens up additional opportunities. Because one of the things that we've learned in delivering modules is that as amazing as they are and as quick as I mean, we have the ability with our studios, which are a single model, even with our duos, which are two models, to have those set in a day and fully installed in about a week. So they're amazing for that. And fully finished ready to go. But you generally need cranes and cranes and power lines do not play well, and once you start getting into removing power lines, it gets very expensive and you start seeing potential timeline extensions of six months or more in order to get those permits. And so it means that with modules we're limited in where we can deliver and with the kit system, it allows us to increase that flexibility because with the kits where we only need about six feet to get into a backyard versus the ability to crane over. And so that's a huge opportunity to address a larger market, as well as to demonstrate the versatility of our production system. Because, again, where we're going is really a design and product agnostic production as a service platform. And so having the ability to do modules, having the ability to do panels really opens up a variety of design possibilities, as well as delivery opportunities that can be customized to the needs of a specific project.
Prefab Review
Got it. So why user facing it all at this point? Just because you need to bring proof of concept? We should talk about your service offering in general to consumers, but, you know, coordinating all these different parts is a lot of work.
Mighty Buildings
That it is.
Prefab Review
It's much more work than just being a technology provider. So, yeah. Why do that?
Mighty Buildings
Yeah, and you're right, because we also do offer a full turnkey experience for our customers where we handle the entitlements, we handle coordination of site work, all of that to make it as easy and as painless as possible. But yeah, you're right, a lot of it basically was to allow us to have the chance to prove the viability of the technology, prove the market fit because most builders and developers tend to be conservative, understandably so, they tend to be risk averse. And so when it comes to new technology, there's some reticence to be the first mover and to be the first one that's taking it up. And so by being able to demonstrate that we can do it with homeowners, it has opened up those other opportunities on the B2B side, especially ever since we announced the Villas project, that interest has gone up even more. That said, we've been talking with some of the biggest builders from the very beginning. And so there are ongoing conversations there that as we demonstrate the ability to deliver and the ability to scale, those will definitely pick up.
Prefab Review
So if I'm thinking about your product lines right now and I'm looking at the fact that you are, it looks like you're also continuing to expand your product line in general.
Mighty Buildings
Exactly. We started with ADUs now we're also offering single family homes. And our goal is hopefully by end of next year to be doing low rise multifamily. So townhouses and three to six story low rise apartment buildings using our new fiber reinforced version of our material that we're moving into a certification later this year.
Prefab Review
And then in terms of your actual, like single family homes and your current products, it sounds obviously you're saying that your technology is infinitely flexible. But if I'm a consumer and I'm a homeowner, like particularly for single, I mean, if you're in the Bay Area, we do a lot of products in the Bay Area. And one of the I would say not my favorite parts of the process is the design review process in some areas. So, like, if I'm trying to build a single family home, even if I really wanted to look this way. Right. Like I might get substantial feedback, how much flexibility if I'm a consumer, do you all sort of so provide me with, you know, design.
Mighty Buildings
Where we are now, it's relatively limited. I mean, particularly because we are operating with state approved plans, which means that we're getting the building permit for at the state level rather than when we get to local level it's more, say, permits for the site work. And then also, as you mentioned, design review and planning and plan checks were zoning purposes.
Prefab Review
And that's true for single family home kits as well? Or are you just kind of on the ADU side?
Mighty Buildings
Well the kits are nice because they have the opportunity to either be certified under the state or with the local authority, depending what makes the most sense, because we also do have the ability or one of the things we're working on is that ability to also to preassemble the kits into modules for sites where that makes sense too. So that also adds to the versatility.
Prefab Review
So that's essentially the same thing as modular.
Mighty Buildings
Exactly. And so one of the things with that versatility is that ability to kind of approach it, the permitting and entitlement process from the route that makes the most sense.
Prefab Review
Right. And because I've found a kit and I don't know what your experiences are. Modular is considerably more complicated to get financed than kits in our experience, just because of the, and maybe it's not different for you, but we we've seen like draw schedules and stuff just be a little, there's a wider variety of lenders we use for when we're doing kit builds then for modular builds.
Mighty Buildings
For ours it's been, I mean well it also depends if the modular is modular or if it's manufactured.
Prefab Review
I mean like non-HUD.
Mighty Buildings
Yeah. For us we haven't noticed a ton of difference yet, but it'll be interesting to see how that changes over time because obviously having those comps makes a huge, huge difference. And so where you're building can often really impact how easy that financing is.
Prefab Review
So in terms of flexibility, just because I mean, I'm looking at the homes on your website right now.
Mighty Buildings
Yeah, it's right now. It is pretty limited.
Prefab Review
So if I wanted to change floor plans within a shell is that kind of, like is it basically only cosmetics, but like any kind of floorplan structure is out?
Mighty Buildings
If you're a B2C customer, we do have some limited customization that we can do. And depending on the project, it's something we can discuss. If it's a developer builder, there's a much greater opportunity to do that because then obviously we're doing a number of units at a time and so more scale and then it makes more sense to go through the process of getting the approval for a new design. But in the future, yeah, the goal is to have a much higher level of customization possible and a lot of those cases will actually be working with builders, developers and kind of doing a white label. Some of them may be custom home builders who are doing larger projects and single family homes, one off. And then some of them will be more developers who are doing a number of units at once. But the goal is eventually to kind of be able to offer that level of versatility, but for where we are, it's not efficient for us to do so yet.
Prefab Review
Looking at your existing product line, can these go on any kind of foundation? Like, I know you're in Oakland and we've done projects in kind of Oakland Hills, Berkeley Hills, and you see a ton of like post and pier foundations and other such things because they sort of it's both kind of the style.
Mighty Buildings
But yeah, I mean, the versatility and all the different soil types. And then, like, if you don't want to do, how much grading do you want to do, or have to do. And so, yes, we designed our modules. I think we already have designs for seven different foundation types, including helical piers and everything we've delivered so far has made sense to do as a slab. But yeah, we do have that ability to adapt to different foundation types depending on the needs of the specific site.
Prefab Review
Got it. So the question we get most, which is riddled with nuance. But that's OK. We'll do the best we can here around cost. So like I'm looking at your website right now and I'm looking at like, let's say, the mighty duo ADU, which is 700 square feet. If we assume that you're installing that in an expensive area, which are probably almost exclusively areas you work in if you're located in Oakland. But, you know, let's say like a flat lot.
Mighty Buildings
Well, I mean we've delivered units to East Oakland. We've delivered units all across the Bay Area, San Diego. So it really doesn't make a difference as far as the neighborhood. We got interest from all over and they're able to deliver.
Prefab Review
Cool, OK, so I just meant like an area. If you were moving units to Riverside County, at least the local area, labor might be a bit different than like.
Mighty Buildings
Yeah, and we do notice that for particularly when we're looking at the full turn-key, we often are able to provide lower final estimates in Southern California than we are for our projects here in Northern California. And that just reflects the nature of the subcontractors for the site work and everything.
Prefab Review
But so let's say I'm talking about building the Duo B, which is like your 700 square foot, one and two bedroom. Can you help me? And I mean, you're really good about sort of breaking down, like starting at prices. But can you sort of explain, like, what you would expect, like a typical build to come out at assuming right, a flat lot And just explain kind of where the cost variabilities are, because I assume the local labor is probably the biggest one.
Mighty Buildings
So, yeah, so the unit itself, a two bedroom, I think we're selling the two modules fully furnished, including a washer-dryer, induction cooktop, dishwasher, everything. High-end finishes, beautiful bathroom, lots of storage. So that is with the two bedroom version, I believe $169,000 for just the unit itself. Right. And then we generally see 30 to 40
Prefab Review
And that is just the module, not including anything else?
Mighty Buildings
Exactly, not counting the site work, not counting the entitlements, not counting any of the delivery, installation. And we generally see about 30 to 40 percent on top of that. So that's where the starting at $255,500 you see on our website for starting out is generally what we see on average. And so that's kind of where that starts. That's going to be more or less what it's going to be for a pretty basic site where it's easy access, flat lot, a community that doesn't have particularly high fees, which obviously now that states cap those in most cases under
Prefab Review
Under seven forty nine, right?
Mighty Buildings
And so where it starts to get expensive is on sites that maybe are on hills, that require grading, that might have a retaining wall that may require or if perhaps it's a site where you've maxed out your utilities and you need to add in another utility box or upgrade your sewer line. So those are obviously things that can add significant costs. But if it's just straightforward, it's pretty, pretty basic. And once the entitlements are in hand, we can have it on the ground and completed in less than a month.
Prefab Review
Are you including solar on those?
Mighty Buildings
They are solar ready and we do have an upgrade available for solar.
Prefab Review
Is it necessary though? I'm sure you're much more knowledgeable on title 24.
Mighty Buildings
Yeah, so it has to be at least solar ready. And then the homeowner is required to install solar, though depending what the shading looks like, that can impact how much solar they're actually required to install. And it also depends because some of our units are actually approved under the previous codes, like I'm ready studio design is basically my studio design. And some of those variations of that actually don't require solar because they were approved under the previous building code and which is good for three years that approval of those ones. So it really varies. But yeah, but we do offer it and we are looking at kind of also offering battery storage to be able to take it off grid because it is, they are pretty efficient. The amount of energy required is relatively low. And so it's yeah, it's definitely an opportunity. And I mean, part of it, like with the Villa project, those are zero net energy because we are both the energy efficiency, but then also the inclusion of solar and the inclusion of battery storage to add not only resiliency, but then further ensure full title 24 compliance and going beyond that to zero net energy.
Prefab Review
And you said all your building is happening out of your Oakland facility right now?
Mighty Buildings
Currently. Correct.
Prefab Review
And obviously, I would say there's one or two companies that we work with that do a bit of construction out of L.A., but part of the idea of prefab or modular, it seems like it's to take advantage of lower cost labor pools. Right. So, you know, as I said, locate your factory in Utah or in Riverside.
Mighty Buildings
Right. I mean, that's why a number of the manufacturers here in California. They're being built in Washington or Idaho.
Prefab Review
Yeah, exactly. I imagine margin matters a little bit for larger builders. So I imagine the ability to just have lower cost inputs probably helps a lot in that stuff. So is that on the roadmap for you all to kind of locate somewhere, in kind of a more rural area probably, or at least a less coastal area?
Mighty Buildings
Sort of. So we're not trying to race to the bottom. What we're doing really is helping the existing labor force build more. Where we're able to capture significant savings per unit is that we can eliminate up to 90 percent of the labor hours and really optimize it so that the human touch is being used for the parts that make sense. In doing so, we're also looking to increase productivity by as much as 20 times. So at the end of the day, we're actually hoping to create more work. And so for us, because of the way we kept our savings, it's not as important to be setting up in rural areas. And in fact, that's one of the things that we can do that you really can't do with traditional prefab and still be cost efficient is that where we are in Oakland. We're in an old Peet's Coffee Warehouse by the Colosseum. So we're in the heart of an industrial center. We were able to find an empty warehouse space that we can take advantage of and not need to build hundreds of thousands of square feet or a million square feet out in a rural or semi-rural area that's far from demand and far from your labor pool. We can actually set up near that demand and use that labor pool while still being efficient. And so that's one of the real big advantages. So our vision is actually a distributed network of factories around the country and around the world, like looking at places like Phoenix, like Detroit, like Pittsburgh, like Seattle, and really being able to set up factories using existing warehouse space. So we're not having to build a bespoke factory, you can actually spin up a factory in three to six months, a relatively low cost, and serve that market and create new jobs for that market. So we're not necessarily trying to avoid the labor. We're actually just trying to think what that labor looks like and what where it makes sense and in order to maximize its value.
Prefab Review
That makes sense. Got it, and then in terms of actually the fulfillment of your existing homes, have you just built a builder network around California to actually do the kind of local foundation and site work and all that stuff?
Mighty Buildings
Yes, we've got a network of contractors that we work with across the state who we've vetted and trained. And we also provide additional tools to make it easy and to help ensure that we get first time right on the foundation every time and make it as cookie cutter and IKEA easy as possible.
Prefab Review
Is there any special training they need to do?
Mighty Buildings
Yeah, no, no special training. I mean, everything they're doing is things that they already know how to do. But we've been looking at how we can help optimize things for them. So providing various forms and things like that just make their lives as easy as possible and also help ensure that it minimizes any rework that's necessary. So in that regard, we're looking at both digital tools, but then also physical things, like what it looks like to create a form or have custom form work for the concrete that we provide to make sure that it is exactly what it's supposed to be. Things like that.
Prefab Review
And you have some details of this on your website. So sorry for the redundancy. From a timing perspective, is the time to build these pretty similar to, you know, most modular and prefab homes?
Mighty Buildings
I mean, we can build the unit in about a week. So once we have permits in hand, we can have a unit fully installed in under a month. I mean, the biggest variable in the entitlement process is the permitting. On our end. We've got it, we've got it locked. Like, once those permits are in hand, we're good to go. We can do it in a month. The issue is that those permit timelines are still incredibly variable. I mean, we've had permits that have taken a week. We've had permits that have taken six months.
Prefab Review
I mean, the state of California has 60 days to get feedback. Right?
Mighty Buildings
They have to take some sort of action within 60 days. And so some of it comes down to , one of the few benefits we've seen from the pandemic is the digitization of planning departments. So that's been a great move. But we're also still dealing with that. They're still dealing with large backlogs and they're doing everything they can. But it's still moving slower than I mean, and from talking with city officials, I mean, it's slower than they want it to be. Like they're not trying to make it slow. It's just the reality of where things are for a lot of projects right now. But they're working on getting better. And part of it is also taking advantage of opportunities like pre-approved plans in places like L.A. and San Jose and others. And so that's one of the methods that we are working on and getting out. And we believe either some have been approved or are in the process of and will be posted there shortly. And so we're looking at ways we can accelerate that way also through just developing that relationship with the local officials because they want to get more housing. I mean, with the regional housing needs allocations as they are, ADUs have become so much more important in helping cities avoid massive fines and lawsuits. So there's real opportunities. But we also have to do education around the fact to build housing programs. We provide an educational packet around who is responsible for what phase of the approval. So there is also an educational component both because of the 3D but because of the familiarity with the approval process for our homes.
Prefab Review
That's awesome and great to learn a little about Mighty Buildings. I want to quickly transition to our fire round where we sort of ask a question to the extent you ca,n answer in one minute or less.
Mighty Buildings
Fire away, I feel like we should be eating hot wings.
Prefab Review
There should be a siren or something. So I guess the first thing is sort of in terms of evaluating sites. I mean, this is a particularly Bay Area, L.A. question we get a lot, which is I'd love to do an ADU. I don't know if my sight is too steep, et cetera. What are the things that homeowners should look for?
Mighty Buildings
Power lines. At least if you're looking to do modular, understanding where the power lines are is a big part of it. Understanding what kind of access you have to the backyard where if you're building with modular, think through like, is there an opportunity, maybe you have a neighbor who has easy access to that location through their driveway or something. And so it's looking for those opportunities. But then also thinking through how steep is it? What kind of soil might you have? What kind of foundation is going to be required? Is it going to require an extensive retaining wall? And these are all things that we help with. So if they're interested and they're not sure, they should reach out to us because we have a wonderful compliance team that does, one of the first things we do, is that we take a look at the site. First we start on Google Maps to do a basic quick understanding of the feasibility, and then we actually send out one of our local partners to confirm what we've learned on the site and look at things like the utilities, understanding the capacity there, whether any upgrades will be required and the viability of the site in terms of delivery and installation.
Prefab Review
OK, that makes sense. In terms of sustainability, we get a lot of press releases from companies claiming a new breakthrough in sustainability and just like in the same way on construction, we get a lot of press releases where people are like, you know, now we cut to one one-thousandth of a millimeter. And this is precision like you've never seen before. So one of the things that we sort of are to figure out is how do we, like, sort of cut through the marketing speak and evaluate what really matters? How would you say on a sustainability process that homeowners who want to kind of live their values, what should they look for?
Mighty Buildings
Yeah, so they should be looking and be asking about how much waste is generated during the construction phase, because that's kind of an often hidden sustainability impact. They should be looking at what kind of energy efficiency does it provide or what are the potential savings to their energy bill? Because, I mean, that's all because the cool thing about sustainability, particularly in terms of energy efficiency and the ability to do zero net energy, is that not only does it have amazing impacts in terms of carbon, I think a zero net energy home in California saves on average about 400 kilograms of carbon a month. So you're looking at like four tons of carbon, almost five tons of carbon a year, but then also looking at about $115 in savings per month on average on the cost. So that's one area, is what's the actual energy efficiency and the performance of it there? And then you should also be looking at things like what's the embodied carbon of the material and what's being used? And I'll admit there, that's one area that we're currently higher than we want to be. But we've also committed to being carbon neutral by 2028 and going beyond that and really shooting for carbon negativity by 2040. So one of the things that we're actively doing right now is we're certifying a new material that has lower carbon. We're identifying new possibilities for further improvements through incorporation of things like recycled materials, as well as continued improvement in terms of strength to allow us to use less material and reduce the carbon impact in that way. But then also what happens at the end of life? Because that's when we're thinking about it, we actually have incorporated lifecycle assessment into our design phase, both in terms of new material as well as new designs. And when we do that, we're not just looking cradle to gate. So we're not just cradle to foundation, we're not looking to just when it's installed, but we're looking all the way to the end of life. And so currently we have the ability to recycle our material, to grind our material up, and we use it as filler. We're looking fifty, a hundred years down the line, but we're already thinking about it. And in the future we're looking at opportunities to go beyond that. And so we're also incorporating obviously design for assembly and for manufacturability and assembly, which is a key part of any manufacturing process, but also adding into that disassembly and reuse. So what's it look like to identify opportunities for reusing the material and end of life? Because it's really important that we're avoiding that landfill at the end, even if it's fifty or a hundred years from now.
Prefab Review
That makes sense. What are the use cases that people are actually using your homes for now? Is it mostly like, "I want a little more room in my house, I want an office" or you've seen people doing this for investment purposes as well?
Mighty Buildings
It runs the gamut. So we've had customers, some who are landlords who want to add an additional unit to an existing rental property to provide more rental options. People who are homeowners who have added a unit to turn that into a rental property and have that income generation people have used them as pool houses, multigenerational living both in terms of younger people moving back, as well as parents kind of moving in as they downsize, guestrooms, as you say, home offices, needing more space. So it really runs the gamut.
Prefab Review
OK, that makes sense. OK, this has been awesome. You definitely passed the fire round.
Mighty Buildings
Oh, good.
Prefab Review
I know you're concerned about that. The final question we ask this to everyone, is what are you excited about for your company or the industry in the near future?
Mighty Buildings
Yeah. So for us I'm really excited about this new project in Rancho Mirage and our step into B2B and really helping become that tool that can unlock the productivity needed while not exacerbating the climate crisis. And more broadly for the industry, I'm really excited by some of the exciting initiatives that are out there, like the Advanced Building Construction Collaborative that's working on either launching or is going to be launched shortly to help unlock productivity in the American offsite construction sector, similar to what was done for silicon chips back in the 90s, because there's a huge new opportunity there. And so it's been really exciting. I'm seeing a lot of stuff happening through, like the Housing Innovation Alliance, a lot of interesting conversations happening about healthy buildings and the build to rent market as kind of growing opportunities, particularly in areas where you have more land and where it's not necessarily competing as much on kind of sensitive environmental areas. So it's definitely some really interesting conversations. And it's great to see the industry really moving towards embracing new technologies as a way to solve the crisis while mitigating those climate crisis impacts.
Prefab Review
That's awesome. Yeah, I agree and we appreciate all the work you all are doing to push this forward. So thanks again, Sam. For more information about Sam and Mighty Buildings, visit mightybuildings.com. And you can also always visit us at prefabreview.com. Thanks again.
Mighty Buildings
Thanks so much, Michael.
Get Our Guide to Buying a Prefab House
Learn how to buy land, select the best house plan, get financing, calculate investment ROI, and more. Save hundreds of hours of research.
We respect your privacy.
Thank you! The guide will be emailed to you soon.
If you want even more support with your project, then signup for Prefab Concierge - our free service where you are paired with a member of our staff who provides you 1:1 support with your potential project -> Learn More
39 에피소드
모든 에피소드
×플레이어 FM에 오신것을 환영합니다!
플레이어 FM은 웹에서 고품질 팟캐스트를 검색하여 지금 바로 즐길 수 있도록 합니다. 최고의 팟캐스트 앱이며 Android, iPhone 및 웹에서도 작동합니다. 장치 간 구독 동기화를 위해 가입하세요.